During the winter of 2018-19 we converted the boiler room in the Engineer’s Garage into a secure storage room.
History
We believe the engineer’s garage was built in the early 1960’s as a place to store and maintain the vehicles that were used by the engineers responsible for the upkeep of the aerial network above Cupar. The building also housed a diesel back up generator and an 11KW electricity sub station. There were 4 giant roller doors for vehicle access. The building was eventually converted into a heated store room with 3 out of the 4 roller door openings being bricked up.
The boiler room housed a Robin Hood General boiler that had been converted to run on kerosene. There is no evidence that the boiler ever ran on coal.
The room itself was in a dire state when we bought the site in 2012. The north wall was covered in green moss, paint was flaking off the walls and the place smelled heavily of kerosene. The door into the room was broken and had been boarded up by the previous owners.
Stripping Out
Our asbestos survey had picked up that the boiler contained asbestos rope, asbestos cement and possible asbestos insulation. For those reasons, the Robin Hood boiler itself was removed and disposed of by our specialist asbestos contractors. I’d have dearly loved to keep it but I have no idea what I would have done with it.
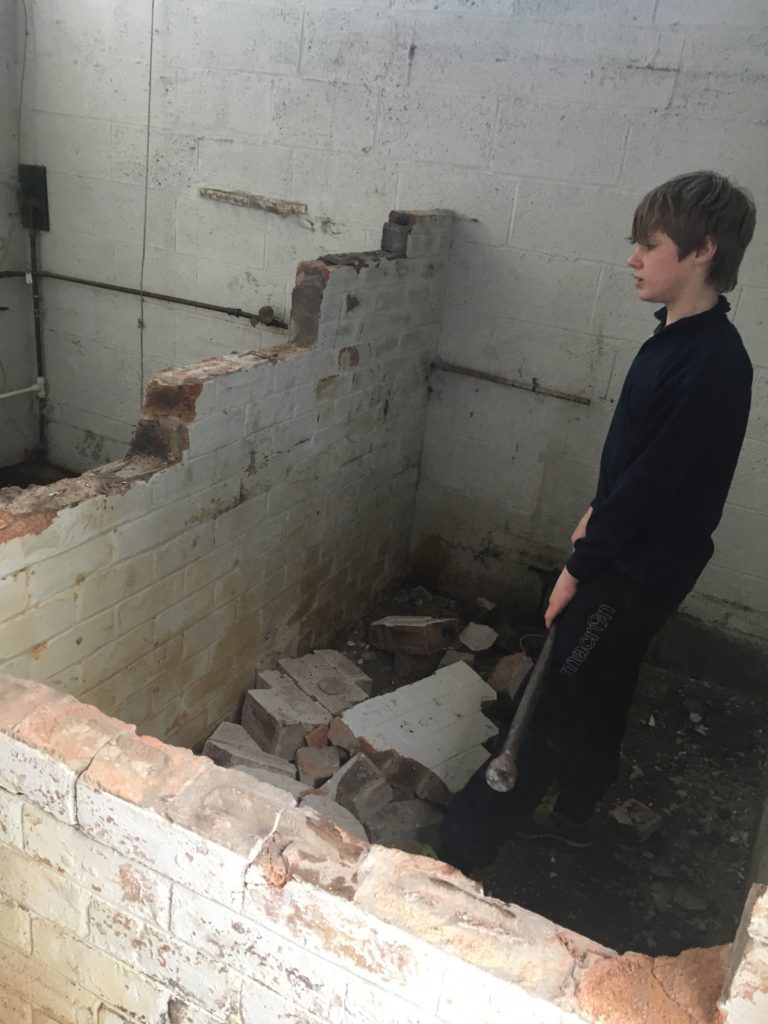
The kerosene tank was removed by another set of specialist contractors who were able to provide safe disposal certificates so we could achieve our site decontamination certificate. The rest of the pipework, electrical fittings and metal were stripped out by me over a couple of weekends.
The brick wall acting as a bund for the kerosene tank was removed by my eldest son who is most happy when swinging a 10lb sledgehammer!
We also removed the lighting, wiring, plumbing and residual pipe and metalwork from the room.
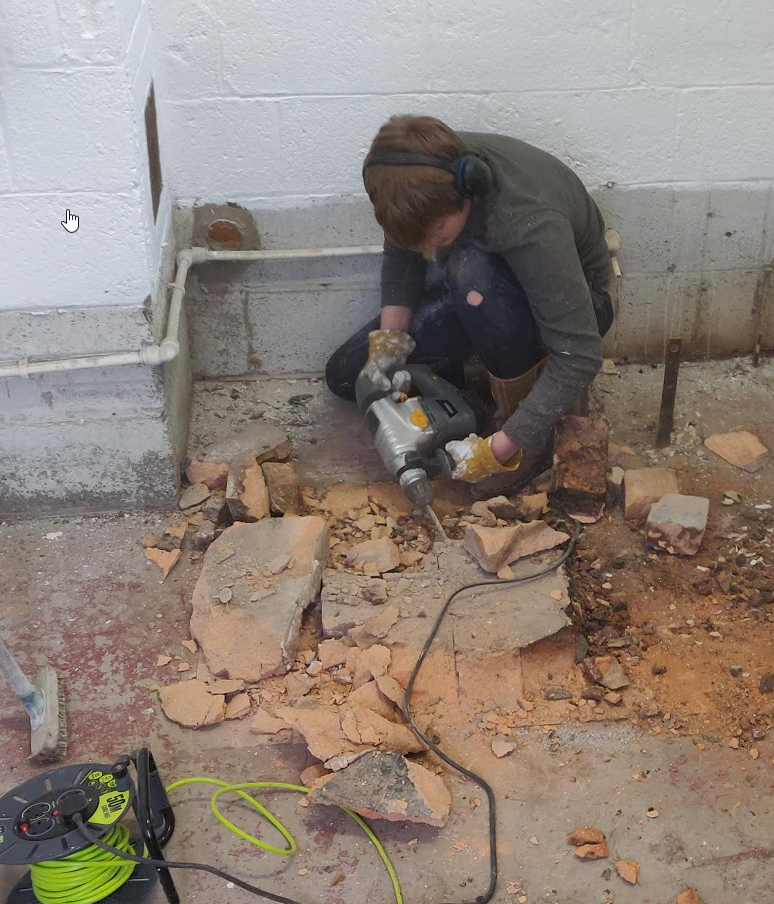
The firebrick plinth that the boiler was sitting on came up relatively easily using a demolition hammer with a broad chisel head, leaving a completely bare room ready for rewiring, filing and painting.
Rewiring
Since we bought Hawklaw in 2012 we have steadily replaced and upgraded the wiring over the entire site. The new garage lighting circuit was waiting just to be brought into the room and the existing external corner lights just needed to be put into conduit and routed around the top of the room.
The new light in the room is a low wattage LED light that responds to both light levels and movement. Technically, the Crabtree toggle switch is redundant, but it’s nice to have something original still in the room.
Decorating
Before we could decorate, the room needed the holes in the block work filled (eg, where the heating and oil pipes entered and exited the room). I brushed the room, including the ceiling with a stiff brush to remove loose paint then hosed the entire room with water. The entire floor slopes gently to a drain so washing the room caused no water issues.
In all, the room took 4 coats of Dulux Weathershield exterior masonry paint. Exterior metal fittings were painted first with red oxide paint before we painted them over with our trademark ‘Hawklaw Grey’ colour. The concrete floor was filled where required with Blackfriar’s concrete repair mortar and lastly, I painted the floor with two coats of Leyland heavy duty floor paint.
The last thing to do was to find a new door for the room.
Selecting a New Door
As we’ll eventually be living on the East side of the site and this room is the furthest away building we have to the West of the site we wanted to select a secure door for this room. This building also gets the brunt of the Westerly winds so a good quality door with multi point locking and excellent seals was essential. After much searching, we selected a Hormann KSi steel security door
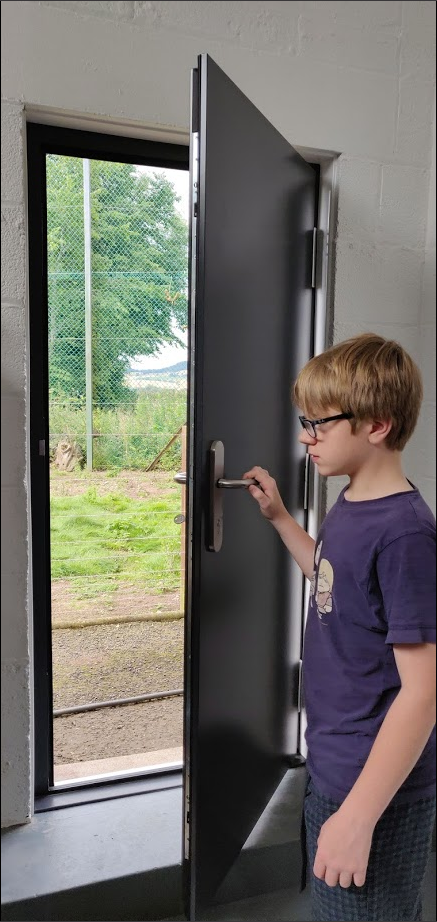
Initially, we thought we wanted an outward opening door as we thought it made sense to have the West wind blow the door against its seal, rather than away from it. We got excellent advice from our door supplier (Oliphant Garage Doors, Cupar, Fife) who assured us that this door would not have any issues with leaking and so far, we’ve been more than happy with it.
The room was without an effective door for nearly eight years so we were very happy to have this fitted and have a functional room once again.
Finishing and Furnishing
We finished the renovation in late January 2019, but didn’t actually get the door fitted until August 2019. It wasn’t long before we’d fully furnished the room with the neatly catalogued contents of our attic.
In all, the renovations cost in the region of £2,500 (including the door) and took me most of my 2018/19 Christmas holidays and a few additional weekends to complete.